Good practice guide for designing an assembly and its components
Assembly process should be carefully designed just as designing parts. A good design of assembly process will lead to a flexible, accurate and low-cost assembly process.
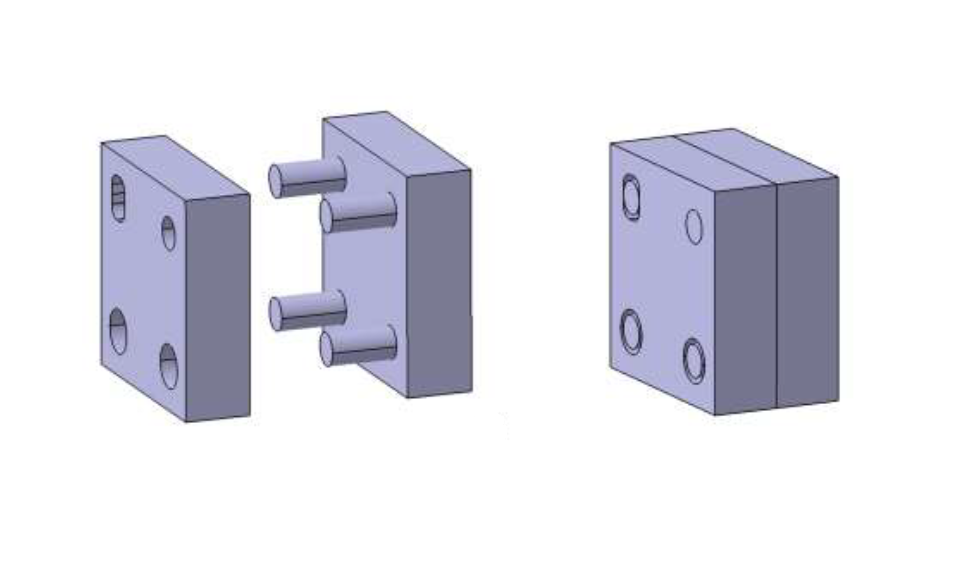
Assembly process should be carefully designed just as designing parts. A good design of assembly process will lead to a flexible, accurate and low-cost assembly process.
Assembly process also requires scientific and practical knowledge to fully understand and design a proper assembly process. Only complete products, assembled from two or more parts, can really provide useful functionalities.
That is why, a product assembly can be said as “the moment of truth” where all parts are joined together and make a complete useful product.
Figure 1 shows an example of how the features of a part are designed by taking consideration to enhance its assembly process.
In figure 1, the features are designed so that the features have inherent mate and contact functionalities (so-called assembly features).
With these inherent and good assembly features, the assembly of the parts can be done without fixture and residual stresses, due to over constraint, can be eliminated.
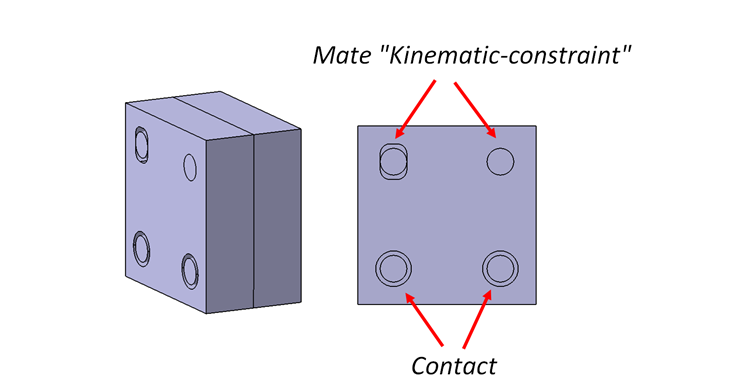
Hence, when designing parts, we have to consider also how the parts will be assembled together to construct a fully functional product and how the parts can be disassembled easily.
Here are a collection of “good practice guide” to design an assembly process that is effective, efficient, and gives economic benefits.
“Good practice guides” to design an assembly process
- The components involved in an assembly process should be standardised. With the use of standardised parts, part interchangeability will be increased and finding supplier of the parts will be easy as well.
- The process production and material costs should be minimised and should satisfy constraints, such as the requirements of a product to be assembled (strength, thermal properties, corrosion resistance, aesthetic and other requirements).
- Manual processes should be minimised. By minimising manual work, the process variation and the number of workers can be minimised as well.
- The interchangeability property of a component should be prioritised.
- The design of an assembly process should consider the production process of the components of the assembly as well as the inspection process of the components. One method used to analyse an assembly before even manufacturing the components is to perform tolerance stack-up analysis.
- Components that involve in an assembly process should be as much as symmetry. A symmetrical design will reduce or eliminate orientation steps in an assembly process.
- A component should be as the base of an assembly. This base component should be designed such that the requirement of jigs and fixtures can be minimised.
- A modular assembly design should be used to ease a complex assembly process by breaking down the assembly process into several easy sub-assembly processes.
- An assembly process that is done automatically should also easily be done by a manual process. This is for cases where the automated system fails, a worker can replace the process while waiting the system is being repaired.
- Increase the tolerance value and surface finish requirements of parts to reduce the production process and inspection costs of the assembly of the parts. However, the given tolerances and surface finish values should satisfy the requirement of the assembly.
- The number of components involved in an assembly should be minimised.
- The part handling systems in an assembly process should have simple but effective designs
- The assigned tolerance values on parts should not be exceeding requirements (too small or too tight). This tight tolerance value will significantly increase the production and inspection cost of the parts.
- Components that construct an assembly should have effective contact, mate and locating features in their design. With these effective mate, contact and locating fixtures, the number of features required can be minimised.
- The use of specialised components or fixtures for an assembly should be minimised. Because, these components usually require special orders, handling and are expensive.
- An assembly process should minimise the number of buffers
- The number of parts in a buffer should be minimised
- We need to use a simple design and method without eliminating functionalities that are required from assembled products.
- An assembly process should use simple and effective processes or steps. The mechanism of the processes or steps should be as simple as possible and requires minimal jig and fixtures.
- Multi-functional components should be utilised in an assembled product. Because, with multi-functional components, the total number of components required to make a functional product can be minimised. By minimising the components constituting an assembly, the total assembly cost and product cost as well can be minimised.
- An assembly process should avoid steps that required precision fitting as much as possible. Precision fitting processes usually require expensive and specialised fixturing systems.
- An assembly should avoid as much as possible the use of many different kind of components.
- An assembly process should avoid over-automated processes. Because, over-automated product will require a very specific system for a specific process and will reduce the flexibility of the assembly process, for example to be re-arranged to accommodate new products.
- Components that constitute an assembly should not have sharp edges. Edges of the components should be designed as dull. One reason is for the safety of the worker doing the assembly.
- Components that have nesting structures should be avoided as much as possible.
- An assembly process should avoid a fastening process that are complex and require long time to process. Hence, the components of the assembly should be designed to have minimal fastening features.
- The components of an assembly should utilised standardised and tested materials in the market. By using this type of material, the supply of the material will be easy so that the cost reduction of the assembly can be obtained.
- An assembly process should use the same type and size of bolts and nuts as much as possible.
- An assembled product should consider the packaging of the product.
- Finally, the dis-assembly process should be designed as easy as the assembly process of a product. This aspect relates to how easy a repair can be done when the product breaks down, for example, the engine assembly of a car.
Conclusion
In this post, a collection of “Good practice guide” that can be followed to design a good assembly process.
Assembly process is “the moment of truth” where all parts are joined together to make a fully functional product that can operate as desired.
Hence, assembly process should be carefully designed and should also have special attentions.
When designing parts constituting a product assembly, we must also considered the assembly process of the parts.
By considering how the parts will be assembled, we can design correct assembly features on the parts. These assembly features will increase the flexibility of the assembly process and the accuracy as well as will reduce the total assembly cost.
We sell all the source files, EXE file, include and LIB files as well as documentation of ellipse fitting by using C/C++, Qt framework, Eigen and OpenCV libraries in this link.
We sell tutorials (containing PDF files, MATLAB scripts and CAD files) about 3D tolerance stack-up analysis based on statistical method (Monte-Carlo/MC Simulation).
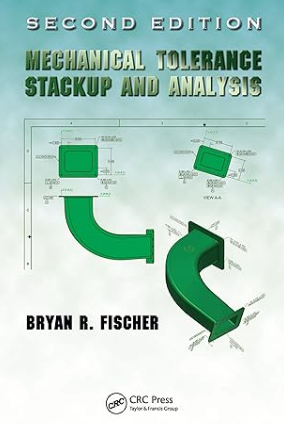