Managing “resistance” to “change” in research and development
In research activities, where we develop something new, there are unknown problems and situations that we must solve.
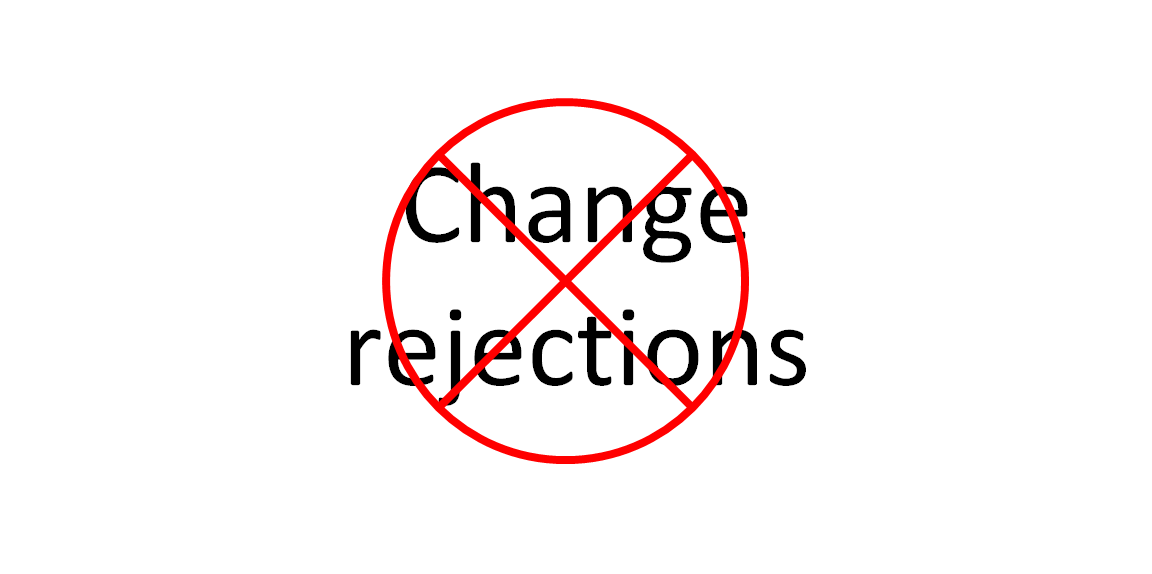
In research activities, where we develop something new, there are unknown problems and situations that we must solve.
To solve these problems, very often we need to “change” something, for example, changing our methods, changing our instruments, changing our team members, changing our collaborators and changing other aspects.
Also, it is very common “change” is always followed by “resistance” from our research teams.
With this “resistance”, instead of moving forward, our research activities will be slow or event going backwards.
In this post, we will discuss how to predict the success of our “change” implementation in our research team and activities.
READ MORE: Research is like a puzzle: Start from anywhere to reach a goal
Do you want to have good research philosophies and improve your research management and productivity?
This book is a humble effort to map well-known and proven principles and rules from various disciplines, such as management, organization decision theory, leadership, strategy, finance and marketing, into a single practical research guide that applies to all disciplines.
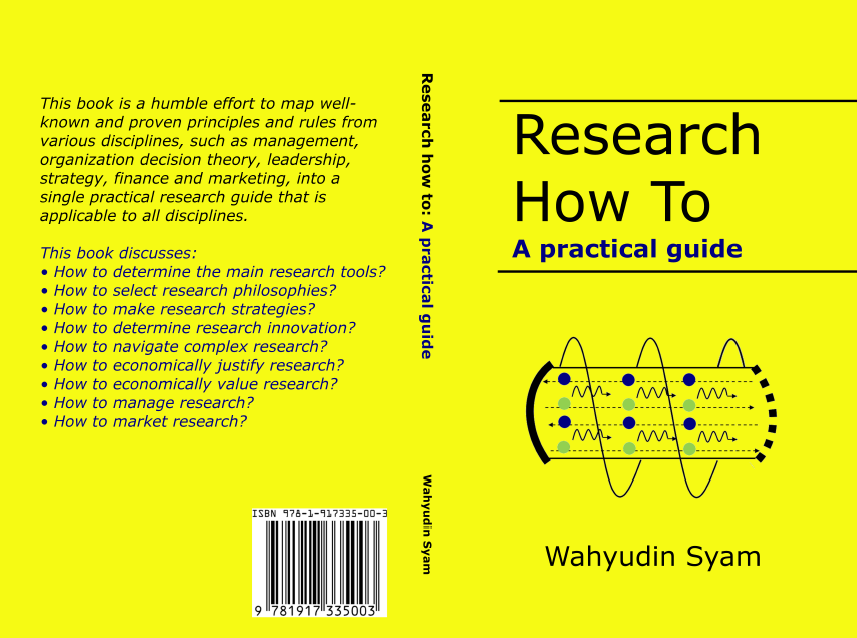
You can also get this book from Rakuten Kobo.
“Change” means uncertainty
To achieve our goals in research and development activities, we must face “change” during the period of our research. For example, we may need to change equipment, obsolete methods, team members, field of research and other aspects.
Of course, this “change” is something that we, as human, always feel uncomfortable with or even scare to embrace the change.
This is a normal situation and will always exist!
Because “change” comes with high uncertainties. We don’t like uncertainty and always want to pursue certainty in every aspect in our lives and plans.
That is, “change” is the only one certainty that we will face in our research and development activities.
Like it or not, we must face it. And yes, resistance is always there.
The question is that, how we can address “resistance of change” and move forward towards our goals?
The answer is that we need to model “change” so that we can estimate the success rate of a change that we will make.
READ MORE: Research how to: A practical guide
Modelling the process of change and its success rate
To reduce the resistance to “change”, we need to quantify the success rate of the “change” that we will make.
To quantify the success rate, we need to model the change success rate.
The formula for “change” to be success is as follows:
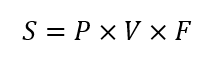
Where:
- S = % success obtained from the change process. This success is basically a dependent variable that we cannot control. Hence, we can control the success of change by controlling the independent variables that affect/control the success of change.
- P = % of pain (regret) of the present. This is the difficulties we are facing at the moment with current situations (such as current equipment, current methodologies and others). The higher the current pain (difficulties), the better people want the change to be, the less the resistant to the change will be, and otherwise.
- V = % of the clarity of the vision. This is about whether people or our team member understand where we are going. What advantages we will get when we embrace and implement the change along its uncertainty.
- F = % of the clarity of the first steps success. This is about the tangible positive results (advantages) we start seeing or feeling. For small companies, we should see the start of positive results of the change within 6-12 months. Meanwhile, for big company, we can expect to start seeing the positive effect within 1 to 3 years. All small achievements we get from implementing “change” should be celebrated by and communicated to all the team member or our people.
From the formula above, the higher the pain (difficulties) we have, the higher the clarity of our vision and the higher the tangibility or realised short-term goal we have, the higher the success rate of the “change” and the lower the resistance we will get, and otherwise.
In order for “change” to be successful (that is, reducing resistance), the “gain” or advantages or positive results obtained from the change should be larger than the cost to apply the change.
To model this, we can use the following formula:
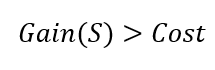
Where:
- Gain(s) is the “gain” or advantages we will get after implementing the “change”.
- Cost is the resources (budget, expertise, man-hour, and other) we need to spend to make or implement the change.
Remember, any “changes” we want to make there will be “resistances” and this always happens. The main idea is we need to minimise resistance.
Also, we should make the change process as fast as we can. Because a slow change process will cause the resistance becomes strong!
READ MORE: A simple and practical way to best select tasks to finish
A brief case study
Let’s us try to implement the success formula of “change” with a brief case study in a manufacturing department.
We will discuss further each independent variables defining the success rate of “change” which are pain (P), clarity of vision (V) and first step success (F) so that we can design/control the variables to increase the success rate of “change” and reduce “resistance” when implementing the “change”.
Let’s the case we are leading a production department with many old but skilled and experienced workers that have worked in our department for such many years.
Suppose we have around 15 people in our department and we are a small manufacturing business.
These workers have been very familiar with current manual machining processes without any automations. They have mastered the skills of tools setting so that they can change settings for certain machining processes rapidly.
However, we want to significantly increase our production rate and should introduce new computer numerically controlled (CNC) machines. These machines require the knowledge of automation and NC-code and some knowledge of spatial coordinate transformations.
Hence, those workers will likely have “resistance” as they need to learn new things and change the way they operate a machine tool, from operating manually to inserting a CNC code and run the machine tool automatically.
Also, they need to learn some automation skills as well as the understanding of spatial coordinate transformations.
Figure 1 below shows the illustration of the change we want to make transitioning from manual machine tools to CNC machine tools.
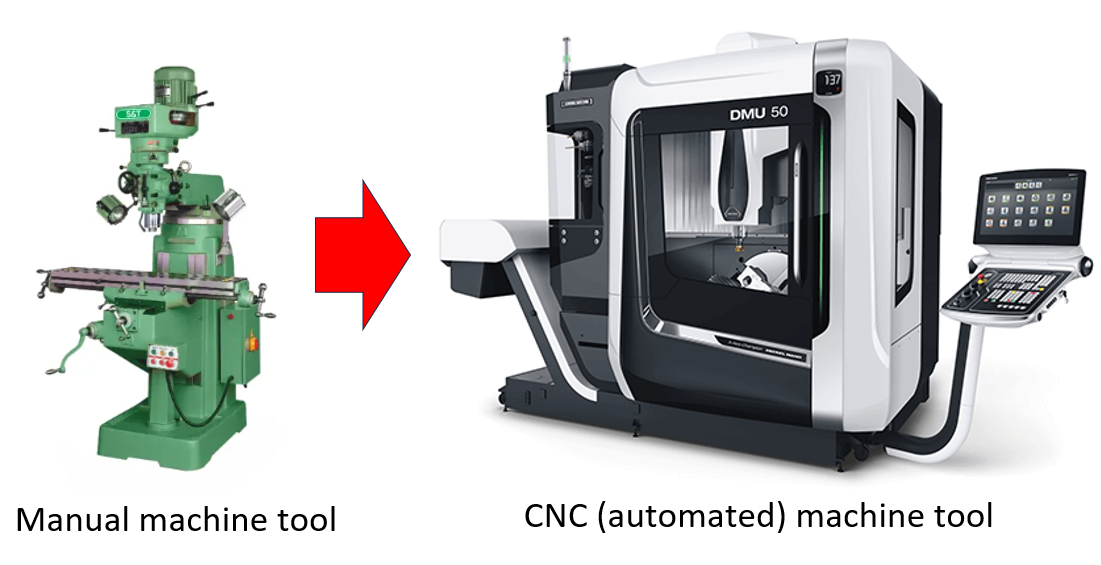
P = % of pain (regret) of the present
To increase the value of this variable percentage, we need to show how low our current production rate is by using manual machine tools.
With this low production rate, we can show how the company profit will be affected and may negatively affect the long-term sustainability of the company.
Not only that, but we also need to show how the part repeatability will be improved and hence the part quality. This quality improvement can boost our competitiveness with other companies.
If we can clearly show this need of improving production rate and quality to sustain the operation of the company, we will increase the percentage of this variable.
Otherwise, if the situation shows that without any changes, our company is already a leader. Hence, this variable value will be very low, and the “resistance” power will be very high.
V = % of the clarity of the vision
For this variable, to increase the value, we should make a clear and good narrative about our vision; What we want to achieve to change from using manual machine tools to using CNC machine tools.
We should not only show that we want to change to CNC machine tools because we want to modernise our facilities.
But we need to clearly explain what our target will be in next few years and in the future. How we want to position our company among competitors.
We should show numbers, for example, we want to improve production rate up to 50% to achieve a profit of certain numbers.
We also need to show that we want to be a leader at certain market segments and hence we need to improve our production rate and also part quality.
F = % of the clarity of the first steps success
Last but not least, this is an important part to increase the success rate of the change we are making.
Since, we are a small business, we should have some initial tangible benefits and improvement within relatively short time, let’s say 6-12 months.
If within this period, there is no tangible benefits, our workers will lose confidence on strategy and their resistance to move to new CNC machine tools will be high as well.
Hence, we need to plan and schedule considering on how we can get some initial tangible benefits for 6 months or so.
These planned benefits can be, for example:
- The workers can learn and have new skills within the first 6 months by giving them extensive technical trainings within the first three months.
- The workers can compare their part quality and part output rate with their previous manual machine tools 3 months after getting the training. Hence after the 6th month since the change started, they can see the real increase in output rate and quality.
- We have a significant reduction in delay of delivering parts to customers within after the first 6-8 months.
- The company can gain financial profits by reducing scrap rate and loss due to delayed delivery.
- And other aspects that we can plan to make sure we can have some tangible benefits during the first 6-12 months since we start the change implementation.
All these three variable combined should be worth it more than the investment (financial and time as well as hassle) we do to make the change (transition from manual to CNC machine tools).
READ MORE: Research management: How to manage knowledge workers
Conclusion
In this post, we describe how “change” is the only thing that is certain in our research and development activities. However, we as human, always resist toward change and sometime even scared from change.
Hence, we need to solve the resistance of change so that people will embrace change and move together toward our shared research goals.
To reduce resistance and increase the success rate of “change”, we have modelled the change to quantify the success rate of the change. With high success rate, we can significantly reduce “resistance” on “change” and move forward our research and development goals.
You may find some interesting items by shopping here.
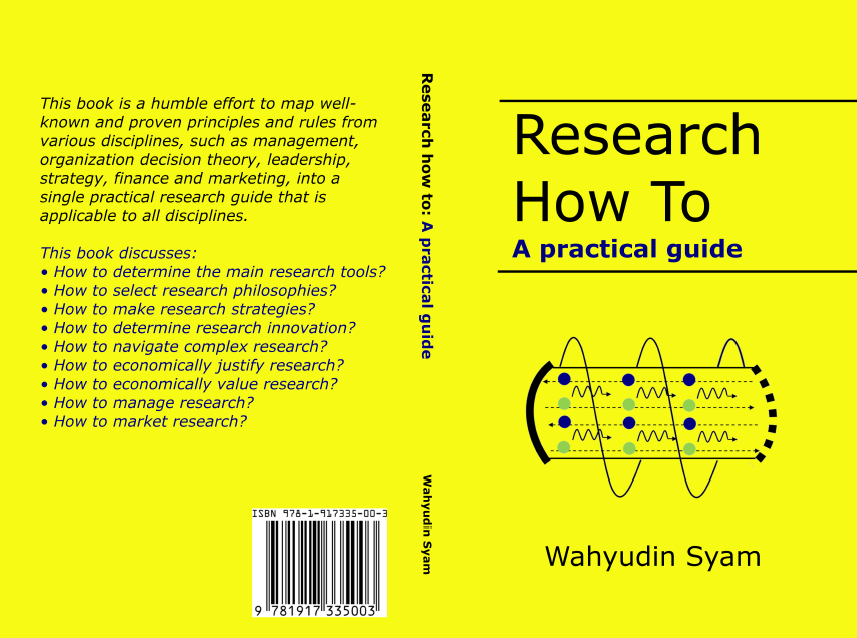